Эмалированная
посуда была неотъемлемой частью
советского быта. Практически в каждом
доме можно было найти эмалированные
кастрюли, чайники и миски с характерным
черным ободком по краю. Но задумывались
ли вы, почему ободок
имел именно
черный цвет и
зачем
вообще он был нужен?
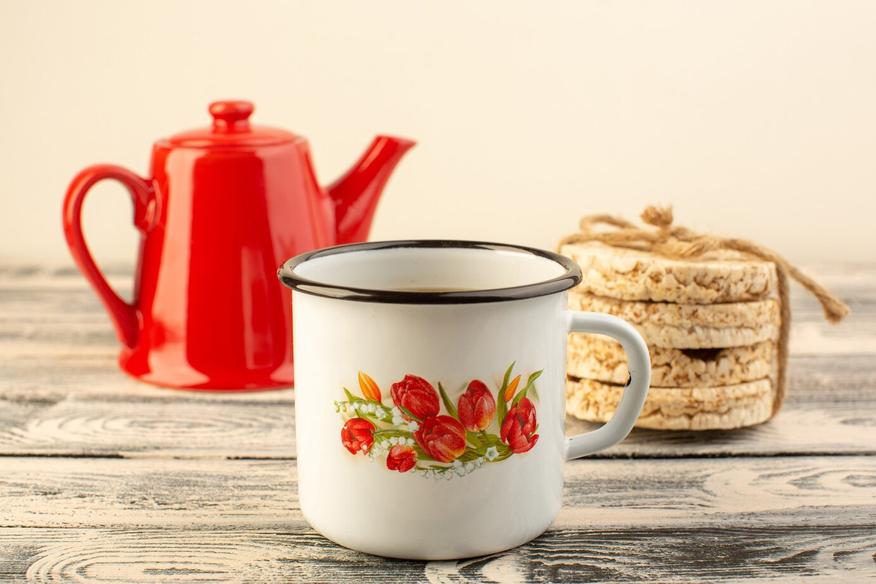
Технология
производства
К началу 80-х гг в Советском Союзе производство эмалированной посуды достигло впечатляющих масштабов. Свыше 280 предприятий производили свыше двухсот млн. единиц продукции ежегодно. Ассортимент был чрезвычайно разнообразен: от привычных чайников и кастрюль до мисок, кружек, тазиков, бидонов и множества других предметов, необходимых в каждом советском доме. Изготовление эмалированной посуды выполнялось по ГОСТам и было практически идентичным на всех советских предприятиях.
Посуда изготавливалась из низкоуглеродистой стали, реже — чугуна или алюминия. Сначала стальные листы нарезали на заготовки, которые затем штамповали или вытягивали на прессах, придавая форму кастрюль, чайников или мисок. Поверхность тщательно очищали пескоструйной обработкой или травлением, чтобы обеспечить лучшее сцепление с эмалью. Эмаль представляла собой стекловидное покрытие из кварцевого песка, соды, буры и оксидов металлов. Эту смесь плавили при 1200°-1400°C, охлаждали и измельчали в порошок или разводили в воде, получая жидкую суспензию (шликер).
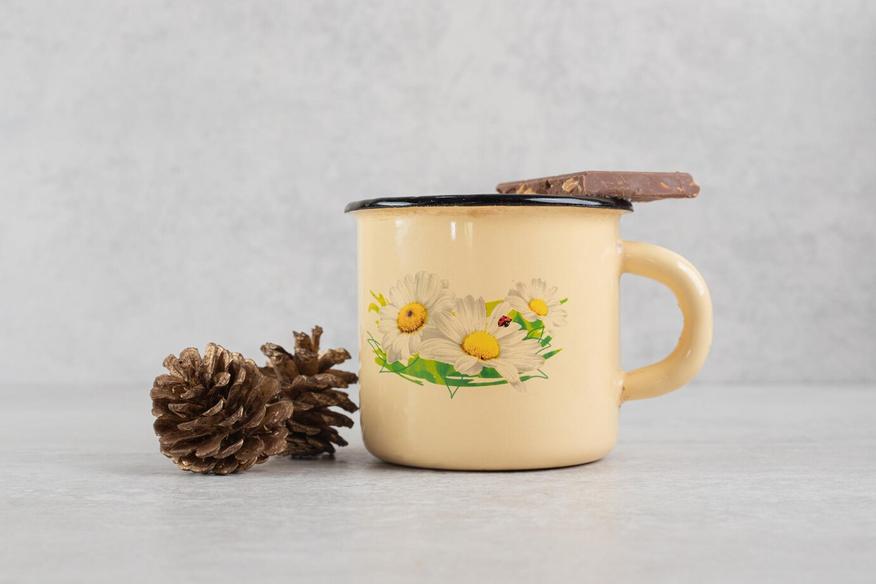
Далее на заготовку наносили грунтовочный слой эмали, улучшающий адгезию. Затем изделия либо окунали в шликер, либо покрывали эмалью распылением, а потом каждый слой сушили при 100°-200°C. После нанесения эмали заготовки помещали в муфельные печи и нагревали до 800°-900°C. Эмаль плавилась, образуя гладкое покрытие. Обжиг проводили в 2-3 этапа для нанесения нескольких слоев, после чего изделия медленно охлаждали. Готовую посуду проверяли на дефекты — сколы, трещины или пузырьки. Брак исправляли или отправляли на переработку. Иногда наносили простые узоры или логотипы завода с помощью деколей, закрепленных при повторном обжиге. Ручная роспись использовалась редко, в основном для экспортных партий.
После прохождения всех этих стадий сложного технологического процесса изделия попадали на контроль качества и, после окончательной проверки, отправлялись на склады готовой продукции, чтобы затем попасть на прилавки магазинов по всей стране.
Почему же ободок был черным
Для основного покрытия посуды использовали белую или цветную эмаль. Для ободков, ручек и изгибов использовали черную эмаль. При этом выбор чёрного цвета для окрашивания был отнюдь не случайным. Изгибы, ободки и ручки были самыми сложными для покрытия: эмаль на этих местах плохо закреплялась из-за напряжений в металле и неровной геометрии. Без защиты края ржавели, а покрытие скалывалось. Решением стала черная эмаль, в составе которой присутствовали оксиды кобальта, никеля и марганца. Эти соединения улучшали сцепление с металлом, повышали устойчивость эмали к высоким температурам обжига и механическим повреждениям, создавая довольно стойкое покрытие. Такой подход продлевал время службы посуды, защищая уязвимые участки от коррозии и сколов.
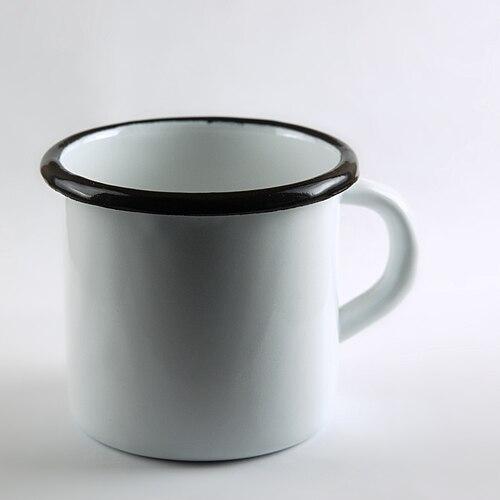
Немаловажным является и экономический аспект. Черный ободок был выгодным решением. Оксиды марганца, кобальта и никеля были доступны и недороги, а черная эмаль хорошо маскировала мелкие дефекты, неровности и микротрещины, сокращая процент брака. Также черный цвет не требовал сложной пигментации и подходил для любой посуды, упрощая процесс на конвейере.
Конечно, несмотря на то, что черный ободок был стандартом, встречались и исключения. Экспортная посуда могла иметь синие, зеленые или серебристые края (за счет оловянного покрытия). Однако такие изделия были редкостью и чаще отправлялись за границу, оставаясь недоступными большинству советских покупателей.
Таким образом, черный ободок — это не часть внешнего оформления, а результат продуманного сочетания химии, технологии и экономики. Черная краска обеспечивала прочность уязвимых краев, а массовое производство по ГОСТам делало посуду доступной и долговечной.
Изображение в превью: